Tecnologia de fusão
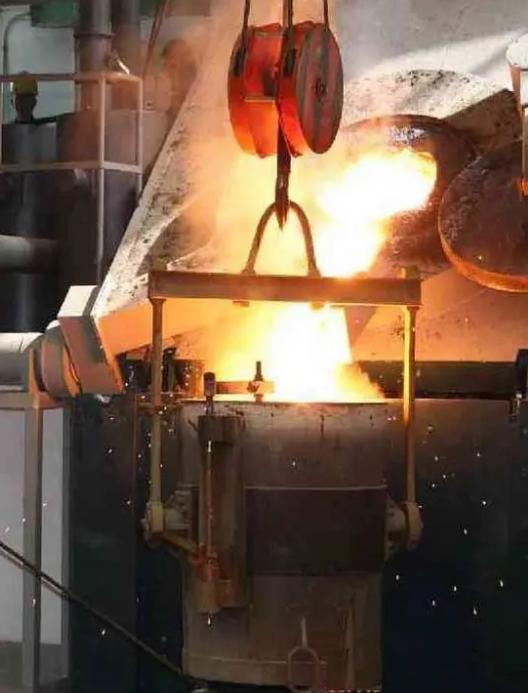
Atualmente, a fundição de produtos de processamento de cobre geralmente adota forno de fundição por indução e também adota fundição em forno reverberatório e fundição em forno de eixo.
A fundição em forno de indução é adequada para todos os tipos de cobre e ligas de cobre, e possui as características de fundição limpa e garante a qualidade do fundido.De acordo com a estrutura do forno, os fornos de indução são divididos em fornos de indução com núcleo e fornos de indução sem núcleo.O forno de indução tubular tem características de alta eficiência de produção e alta eficiência térmica e é adequado para fusão contínua de uma única variedade de cobre e ligas de cobre, como cobre vermelho e latão.O forno de indução sem núcleo possui características de rápida velocidade de aquecimento e fácil substituição de variedades de liga.É adequado para fundir cobre e ligas de cobre com alto ponto de fusão e diversas variedades, como bronze e cuproníquel.
O forno de indução a vácuo é um forno de indução equipado com um sistema de vácuo, adequado para fundir cobre e ligas de cobre que são fáceis de inalar e oxidar, como cobre livre de oxigênio, bronze de berílio, bronze de zircônio, bronze de magnésio, etc.
A fundição em forno reverberatório pode refinar e remover impurezas do fundido e é usada principalmente na fundição de sucata de cobre.O forno de eixo é um tipo de forno de fusão rápida e contínua, que tem as vantagens de alta eficiência térmica, alta taxa de fusão e desligamento conveniente do forno.Pode ser controlado;não há processo de refino, portanto, a grande maioria das matérias-primas deve ser cobre catódico.Os fornos de eixo são geralmente usados com máquinas de lingotamento contínuo para lingotamento contínuo e também podem ser usados com fornos de retenção para lingotamento semicontínuo.
A tendência de desenvolvimento da tecnologia de produção de fundição de cobre reflete-se principalmente na redução da perda de queima de matérias-primas, na redução da oxidação e inalação do fundido, na melhoria da qualidade do fundido e na adoção de alta eficiência (a taxa de fusão do forno de indução é maior superior a 10 t/h), grande escala (a capacidade do forno de indução pode ser superior a 35 t/conjunto), longa vida (a vida útil do revestimento é de 1 a 2 anos) e economia de energia (o consumo de energia do forno de indução o forno é inferior a 360 kW h/t), o forno de retenção está equipado com um dispositivo de desgaseificação (desgaseificação de gás CO) e o forno de indução O sensor adota estrutura de spray, o equipamento de controle elétrico adota tiristor bidirecional mais fonte de alimentação de conversão de frequência, o pré-aquecimento do forno, monitoramento da condição do forno e campo de temperatura refratária e sistema de alarme, o forno de retenção é equipado com um dispositivo de pesagem e o controle de temperatura é mais preciso.
Equipamento de Produção - Linha de Corte
A produção da linha de corte de tiras de cobre é uma linha de produção contínua de corte e corte que alarga a bobina larga através do desbobinador, corta a bobina na largura necessária através da máquina de corte e a rebobina em várias bobinas através do enrolador. Use um guindaste para armazenar os rolos na prateleira de armazenamento
↓
(Carregamento de carro) Use o carrinho de alimentação para colocar manualmente o rolo de material no tambor desbobinador e apertá-lo
↓
(Desbobinador e rolo de pressão anti-afrouxamento) Desenrole a bobina com a ajuda da guia de abertura e rolo de pressão
↓
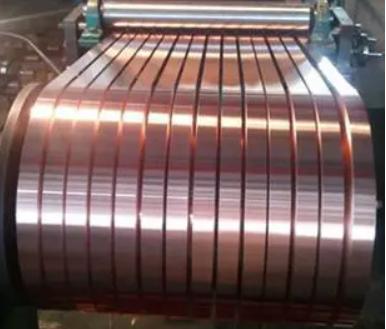
(NO·1 looper e ponte oscilante) armazenamento e buffer
↓
(Dispositivo de guia de borda e rolo de pressão) Os rolos verticais guiam a folha nos rolos de pressão para evitar desvios, a largura e o posicionamento do rolo de guia vertical são ajustáveis
↓
(Máquina de corte) entre na máquina de corte para posicionamento e corte
↓
(Sede rotativa de troca rápida) Troca do grupo de ferramentas
↓
(Dispositivo de enrolamento de sucata) Corte a sucata
↓(Mesa guia da extremidade de saída e batente da cauda da bobina) Introduzir o looper NO.2
↓
(ponte giratória e laçador NO.2) armazenamento de material e eliminação de diferença de espessura
↓
(Dispositivo de separação da tensão da placa de pressão e do eixo de expansão de ar) fornece força de tensão, separação da placa e da correia
↓
(Tesoura de corte, dispositivo de medição de comprimento de direção e mesa guia) medição de comprimento, segmentação de comprimento fixo de bobina, guia de passagem de fita
↓
(enrolador, dispositivo de separação, dispositivo de placa de pressão) tira separadora, enrolamento
↓
(descarga de caminhão, embalagem) fita de cobre para descarga e embalagem
Tecnologia de laminação a quente
A laminação a quente é usada principalmente para laminação de tarugos de lingotes para produção de folhas, tiras e folhas metálicas.
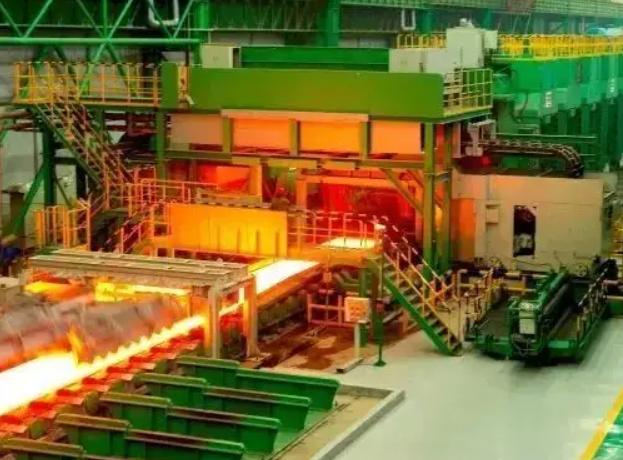
As especificações de lingotes para laminação de tarugos devem considerar fatores como variedade do produto, escala de produção, método de fundição, etc., e estão relacionadas às condições do equipamento de laminação (como abertura do rolo, diâmetro do rolo, pressão de laminação permitida, potência do motor e comprimento da mesa do rolo). , etc.Geralmente, a relação entre a espessura do lingote e o diâmetro do rolo é de 1: (3,5 ~ 7): a largura é geralmente igual ou várias vezes a largura do produto acabado, e a largura e a quantidade de corte devem ser adequadamente considerado.Geralmente, a largura da laje deve ser 80% do comprimento do corpo do rolo.O comprimento do lingote deve ser razoavelmente considerado de acordo com as condições de produção.De modo geral, sob a premissa de que a temperatura final de laminação a quente pode ser controlada, quanto mais longo o lingote, maior será a eficiência e o rendimento da produção.
As especificações do lingote de plantas de processamento de cobre de pequeno e médio porte são geralmente (60 ~ 150) mm × (220 ~ 450) mm × (2.000 ~ 3.200) mm, e o peso do lingote é de 1,5 ~ 3 t;as especificações do lingote de grandes plantas de processamento de cobre Geralmente, é (150 ~ 250) mm × (630 ~ 1250) mm × (2400 ~ 8000) mm, e o peso do lingote é de 4,5 ~ 20 t.
Durante a laminação a quente, a temperatura da superfície do rolo aumenta acentuadamente no momento em que o rolo entra em contato com a peça rolante de alta temperatura.A expansão térmica repetida e a contração a frio causam rachaduras e rachaduras na superfície do rolo.Portanto, o resfriamento e a lubrificação devem ser realizados durante a laminação a quente.Normalmente, água ou uma emulsão de concentração mais baixa é usada como meio de resfriamento e lubrificação.A taxa total de trabalho da laminação a quente é geralmente de 90% a 95%.A espessura da tira laminada a quente é geralmente de 9 a 16 mm.O fresamento superficial da tira após a laminação a quente pode remover camadas superficiais de óxido, intrusões de incrustações e outros defeitos superficiais produzidos durante a fundição, aquecimento e laminação a quente.De acordo com a gravidade dos defeitos superficiais da tira laminada a quente e as necessidades do processo, a quantidade de fresagem de cada lado é de 0,25 a 0,5 mm.
Os laminadores a quente são geralmente laminadores reversíveis de duas ou quatro alturas.Com o alargamento do lingote e o alongamento contínuo do comprimento da tira, o nível de controle e a função do laminador a quente têm uma tendência de melhoria e melhoria contínua, como a utilização de controle automático de espessura, dobradeiras hidráulicas, dianteiras e traseiras rolos verticais, apenas rolos de resfriamento sem resfriamento Dispositivo de laminação, controle de coroa de rolo TP (Taper Pis-ton Roll), têmpera on-line (têmpera) após laminação, bobinamento on-line e outras tecnologias para melhorar a uniformidade da estrutura e propriedades da tira e obter melhor placa.
Tecnologia de fundição
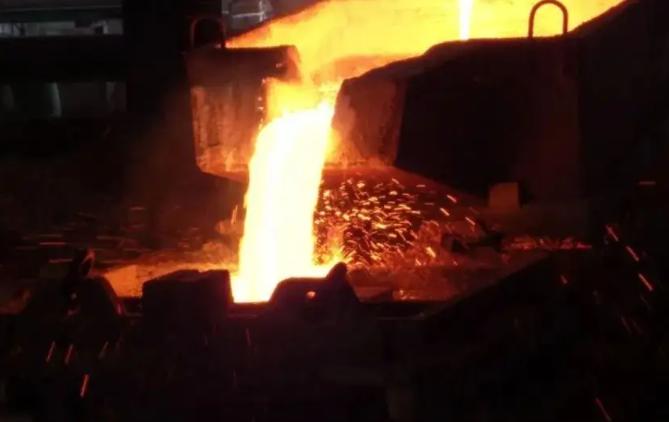
A fundição de cobre e ligas de cobre é geralmente dividida em: fundição semicontínua vertical, fundição vertical completa, fundição contínua horizontal, fundição contínua ascendente e outras tecnologias de fundição.
A. Fundição Semi-Contínua Vertical
A fundição vertical semicontínua tem características de equipamento simples e produção flexível, e é adequada para fundir vários lingotes redondos e planos de cobre e ligas de cobre.O modo de transmissão da máquina de fundição semicontínua vertical é dividido em hidráulico, parafuso de avanço e cabo de aço.Como a transmissão hidráulica é relativamente estável, ela tem sido mais utilizada.O cristalizador pode ser vibrado com diferentes amplitudes e frequências conforme necessário.Atualmente, o método de fundição semicontínua é amplamente utilizado na produção de lingotes de cobre e ligas de cobre.
B. Fundição Contínua Completa Vertical
O lingotamento contínuo completo vertical tem características de grande rendimento e alto rendimento (cerca de 98%), adequado para produção contínua e em larga escala de lingotes com uma única variedade e especificação, e está se tornando um dos principais métodos de seleção para fusão e fundição processo em modernas linhas de produção de tiras de cobre em larga escala.O molde de fundição contínua vertical completo adota controle automático de nível de líquido a laser sem contato.A máquina de fundição geralmente adota fixação hidráulica, transmissão mecânica, serragem de cavacos a seco refrigerada a óleo on-line e coleta de cavacos, marcação automática e inclinação do lingote.A estrutura é complexa e o grau de automação é alto.
C. Fundição Contínua Horizontal
A fundição contínua horizontal pode produzir tarugos e tarugos de arame.
A fundição contínua horizontal de tiras pode produzir tiras de cobre e ligas de cobre com espessura de 14-20 mm.As tiras nesta faixa de espessura podem ser laminadas diretamente a frio sem laminação a quente, por isso são frequentemente usadas para produzir ligas que são difíceis de laminar a quente (como estanho. Bronze fosforoso, latão de chumbo, etc.), também podem produzir latão, tiras de liga de cuproníquel e cobre de baixa liga.Dependendo da largura da tira de fundição, a fundição contínua horizontal pode fundir de 1 a 4 tiras ao mesmo tempo.As máquinas de fundição contínua horizontais comumente usadas podem fundir duas tiras ao mesmo tempo, cada uma com largura inferior a 450 mm, ou fundir uma tira com largura de tira de 650-900 mm.A tira de fundição contínua horizontal geralmente adota o processo de fundição de puxar-parar-empurrar reverso, e há linhas de cristalização periódicas na superfície, que geralmente devem ser eliminadas por fresagem.Existem exemplos nacionais de tiras de cobre de alta superfície que podem ser produzidas trefilando e fundindo tarugos de tiras sem fresagem.
A fundição contínua horizontal de tarugos de tubos, hastes e fios pode fundir de 1 a 20 lingotes ao mesmo tempo, de acordo com diferentes ligas e especificações.Geralmente, o diâmetro da barra ou do fio bruto é de 6 a 400 mm, e o diâmetro externo do tubo vazio é de 25 a 300 mm.A espessura da parede é de 5 a 50 mm e o comprimento lateral do lingote é de 20 a 300 mm.As vantagens do método de fundição contínua horizontal são que o processo é curto, o custo de fabricação é baixo e a eficiência de produção é alta.Ao mesmo tempo, é também um método de produção necessário para alguns materiais de liga com baixa trabalhabilidade a quente.Recentemente, é o principal método para fazer tarugos de produtos de cobre comumente usados, como tiras de bronze estanho-fósforo, tiras de liga de zinco-níquel e tubos de ar condicionado de cobre desoxidado com fósforo.métodos de produção.
As desvantagens do método de produção de fundição contínua horizontal são: as variedades de liga adequadas são relativamente simples, o consumo do material de grafite na luva interna do molde é relativamente grande e a uniformidade da estrutura cristalina da seção transversal do lingote não é fácil de controlar.A parte inferior do lingote é continuamente resfriada devido ao efeito da gravidade, que fica próxima à parede interna do molde, e os grãos são mais finos;a parte superior se deve à formação de entreferros e à alta temperatura de fusão, o que provoca o atraso na solidificação do lingote, o que retarda a taxa de resfriamento e faz com que a histerese de solidificação do lingote.A estrutura cristalina é relativamente grosseira, o que é especialmente óbvio para lingotes de grande porte.Tendo em vista as deficiências acima, o método de fundição por flexão vertical com tarugo está atualmente sendo desenvolvido.Uma empresa alemã usou um fundidor contínuo de flexão vertical para testar tiras de bronze-estanho (16-18) mm × 680 mm, como DHP e CuSn6, a uma velocidade de 600 mm/min.
D. Fundição Contínua Ascendente
A fundição contínua ascendente é uma tecnologia de fundição que se desenvolveu rapidamente nos últimos 20 a 30 anos e é amplamente utilizada na produção de tarugos de fio para fio-máquina de cobre brilhante.Ele utiliza o princípio da fundição por sucção a vácuo e adota a tecnologia stop-pull para realizar a fundição contínua de múltiplas cabeças.Possui características de equipamentos simples, pequeno investimento, menor perda de metal e procedimentos de baixa poluição ambiental.A fundição contínua ascendente é geralmente adequada para a produção de tarugos de cobre vermelho e fios de cobre isentos de oxigênio.A nova conquista desenvolvida nos últimos anos é a sua popularização e aplicação em blanks de tubos de grande diâmetro, latão e cuproníquel.Atualmente, foi desenvolvida uma unidade de lingotamento contínuo ascendente com uma produção anual de 5.000 t e um diâmetro superior a Φ100 mm;Foram produzidos tarugos de fio de liga ternária de latão comum binário e cobre branco-zinco, e o rendimento dos tarugos de fio pode chegar a mais de 90%.
E. Outras técnicas de fundição
A tecnologia de tarugos de lingotamento contínuo está em desenvolvimento.Ele supera defeitos como marcas formadas na superfície externa do tarugo devido ao processo stop-pull do lingotamento contínuo ascendente, e a qualidade da superfície é excelente.E devido às suas características de solidificação quase direcionais, a estrutura interna é mais uniforme e pura, portanto o desempenho do produto também é melhor.A tecnologia de produção de tarugo de fio de cobre de fundição contínua tipo correia tem sido amplamente utilizada em grandes linhas de produção acima de 3 toneladas.A área da seção transversal da placa é geralmente superior a 2.000 mm2, e é seguida por um laminador contínuo com alta eficiência de produção.
A fundição eletromagnética foi tentada em meu país já na década de 1970, mas a produção industrial não foi realizada.Nos últimos anos, a tecnologia de fundição eletromagnética fez grandes progressos.Atualmente, lingotes de cobre isentos de oxigênio de Φ200 mm foram fundidos com sucesso com superfície lisa.Ao mesmo tempo, o efeito de agitação do campo eletromagnético no fundido pode promover a exaustão e a remoção de escória, e pode ser obtido cobre livre de oxigênio com um teor de oxigênio inferior a 0,001%.
A direção da nova tecnologia de fundição de liga de cobre é melhorar a estrutura do molde através de solidificação direcional, solidificação rápida, formação semissólida, agitação eletromagnética, tratamento metamórfico, controle automático do nível de líquido e outros meios técnicos de acordo com a teoria da solidificação., densificação, purificação e realização de operação contínua e formação quase final.
No longo prazo, a fundição de cobre e ligas de cobre será a coexistência da tecnologia de fundição semicontínua e da tecnologia de fundição contínua completa, e a proporção de aplicação da tecnologia de fundição contínua continuará a aumentar.
Tecnologia de laminação a frio
De acordo com a especificação da tira laminada e o processo de laminação, a laminação a frio é subdividida em floração, laminação intermediária e laminação de acabamento.O processo de laminação a frio da tira fundida com espessura de 14 a 16 mm e do tarugo laminado a quente com espessura de cerca de 5 a 16 mm a 2 a 6 mm é chamado de florescimento, e o processo de continuar a reduzir a espessura do a peça laminada é chamada de laminação intermediária., a laminação a frio final para atender aos requisitos do produto acabado é chamada de laminação de acabamento.
O processo de laminação a frio precisa controlar o sistema de redução (taxa de processamento total, taxa de processamento de passagem e taxa de processamento do produto acabado) de acordo com diferentes ligas, especificações de laminação e requisitos de desempenho do produto acabado, selecionar e ajustar razoavelmente o formato do rolo e selecionar razoavelmente a lubrificação método e lubrificante.Medição e ajuste de tensão.
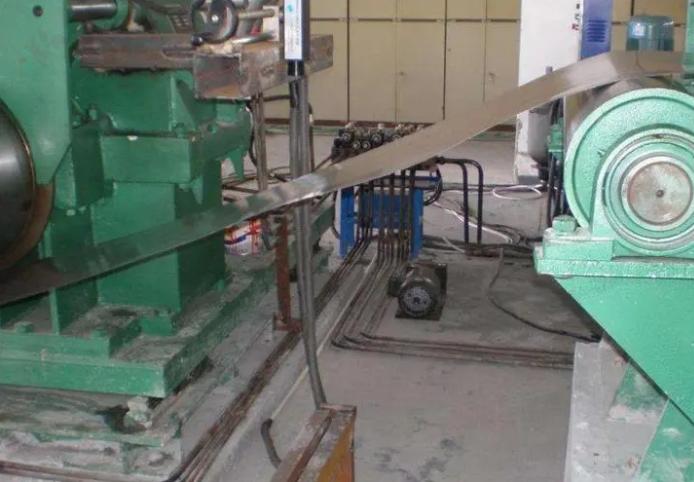
Os laminadores a frio geralmente usam laminadores reversíveis de quatro ou múltiplas alturas.Os laminadores a frio modernos geralmente usam uma série de tecnologias, como dobra hidráulica positiva e negativa de rolos, controle automático de espessura, pressão e tensão, movimento axial de rolos, resfriamento segmentar de rolos, controle automático de formato de placa e alinhamento automático de peças laminadas. , para que a precisão da tira possa ser melhorada.Até 0,25±0,005 mm e dentro de 5I do formato da placa.
A tendência de desenvolvimento da tecnologia de laminação a frio se reflete no desenvolvimento e aplicação de laminadores multi-rolos de alta precisão, velocidades de laminação mais altas, controle mais preciso da espessura e forma da tira e tecnologias auxiliares, como resfriamento, lubrificação, bobinamento, centralização e laminação rápida. mudar.refinamento, etc
Equipamento de Produção - Forno Bell
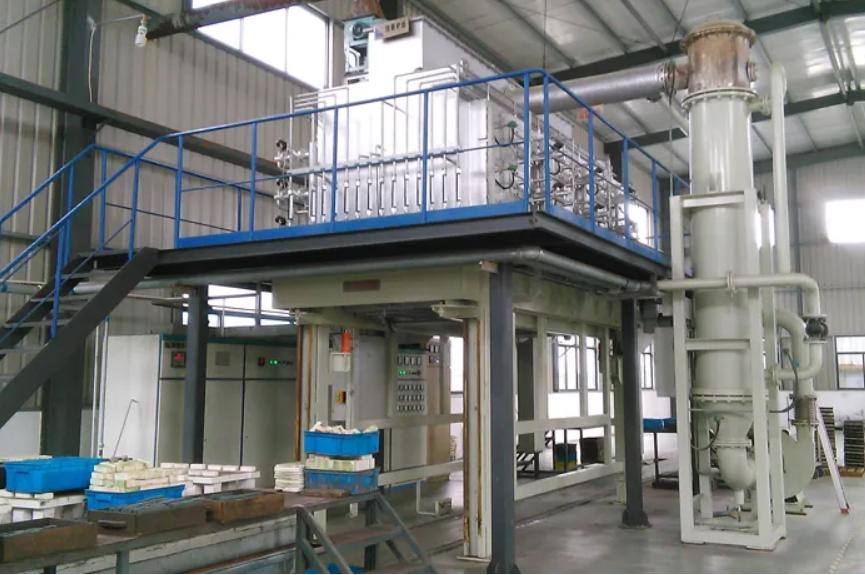
Fornos de redoma e fornos de elevação são geralmente usados na produção industrial e em testes piloto.Geralmente, a potência é grande e o consumo de energia é grande.Para empresas industriais, o material do forno de elevação Luoyang Sigma é fibra cerâmica, que tem bom efeito de economia de energia, baixo consumo de energia e baixo consumo de energia.Economize eletricidade e tempo, o que é benéfico para aumentar a produção.
Há vinte e cinco anos, a BRANDS alemã e a Philips, uma empresa líder na indústria de fabricação de ferrite, desenvolveram em conjunto uma nova máquina de sinterização.O desenvolvimento deste equipamento atende às necessidades especiais da indústria de ferrite.Durante este processo, o Forno Bell BRANDS é continuamente atualizado.
Ele está atento às necessidades de empresas de renome mundial como Philips, Siemens, TDK, FDK, etc., que também se beneficiam muito dos equipamentos de alta qualidade da BRANDS.
Devido à alta estabilidade dos produtos produzidos pelos fornos tipo sino, os fornos tipo sino tornaram-se as principais empresas na indústria de produção profissional de ferrite.Há vinte e cinco anos, o primeiro forno fabricado pela BRANDS ainda produz produtos de alta qualidade para a Philips.
A principal característica do forno de sinterização oferecido pelo forno tipo sino é sua alta eficiência.Seu sistema de controle inteligente e outros equipamentos formam uma unidade funcional completa, que pode atender plenamente aos requisitos de última geração da indústria de ferrite.
Os clientes de fornos tipo sino podem programar e armazenar qualquer perfil de temperatura/atmosfera necessário para produzir produtos de alta qualidade.Além disso, os clientes também podem produzir quaisquer outros produtos dentro do prazo, de acordo com as necessidades reais, reduzindo assim os prazos de entrega e os custos.O equipamento de sinterização deve ter boa ajustabilidade para produzir uma variedade de produtos diferentes para se adaptar continuamente às necessidades do mercado.Isto significa que os produtos correspondentes devem ser produzidos de acordo com as necessidades de cada cliente.
Um bom fabricante de ferrite pode produzir mais de 1000 ímãs diferentes para atender às necessidades especiais dos clientes.Estes requerem a capacidade de repetir o processo de sinterização com alta precisão.Os sistemas de forno tipo campânula tornaram-se fornos padrão para todos os produtores de ferrite.
Na indústria de ferrita, esses fornos são usados principalmente para ferrite de baixo consumo de energia e alto valor μ, especialmente na indústria de comunicações.É impossível produzir machos de alta qualidade sem um forno tipo sino.
O forno tipo sino requer apenas alguns operadores durante a sinterização, a carga e a descarga podem ser concluídas durante o dia e a sinterização pode ser concluída à noite, permitindo a redução de pico de eletricidade, o que é muito prático na situação atual de escassez de energia.Os fornos de redoma produzem produtos de alta qualidade e todos os investimentos adicionais são rapidamente recuperados devido aos produtos de alta qualidade.O controle de temperatura e atmosfera, o projeto do forno e o controle do fluxo de ar dentro do forno estão perfeitamente integrados para garantir aquecimento e resfriamento uniformes do produto.O controle da atmosfera do forno durante o resfriamento está diretamente relacionado à temperatura do forno e pode garantir um teor de oxigênio de 0,005% ou até inferior.E estas são coisas que os nossos concorrentes não podem fazer.
Graças ao completo sistema de entrada de programação alfanumérica, longos processos de sinterização podem ser facilmente replicados, garantindo assim a qualidade do produto.Ao vender um produto, é também um reflexo da qualidade do produto.
Tecnologia de tratamento térmico
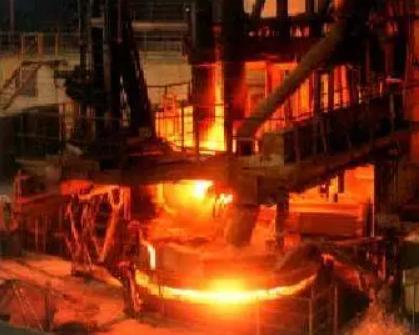
Alguns lingotes de liga (tiras) com segregação dendrítica severa ou tensão de fundição, como o bronze estanho-fósforo, precisam passar por um recozimento de homogeneização especial, que geralmente é realizado em um forno de redoma.A temperatura de recozimento de homogeneização está geralmente entre 600 e 750°C.
Atualmente, a maior parte do recozimento intermediário (recozimento de recristalização) e do recozimento acabado (recozimento para controlar o estado e desempenho do produto) de tiras de liga de cobre são recozidos brilhantes por proteção de gás.Os tipos de forno incluem forno de redoma, forno de almofada de ar, forno de tração vertical, etc. O recozimento oxidativo está sendo eliminado.
A tendência de desenvolvimento da tecnologia de tratamento térmico se reflete no tratamento de solução on-line de laminação a quente de materiais de liga reforçados por precipitação e na subsequente tecnologia de tratamento térmico de deformação, recozimento brilhante contínuo e recozimento de tensão em uma atmosfera protetora.
Têmpera — O tratamento térmico de envelhecimento é usado principalmente para o fortalecimento tratável termicamente de ligas de cobre.Através do tratamento térmico, o produto altera sua microestrutura e obtém as propriedades especiais exigidas.Com o desenvolvimento de ligas de alta resistência e alta condutividade, o processo de tratamento térmico por têmpera e envelhecimento será mais aplicado.O equipamento de tratamento de envelhecimento é aproximadamente igual ao equipamento de recozimento.
Tecnologia de Extrusão
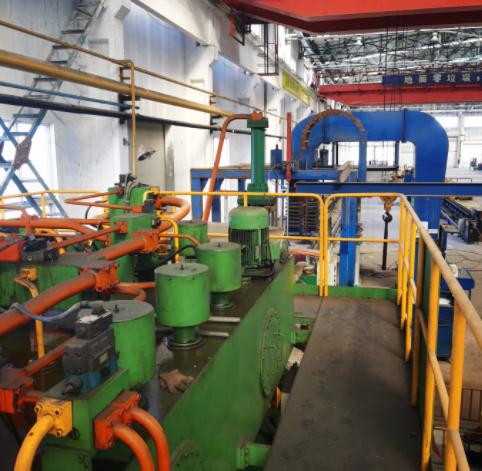
A extrusão é um método maduro e avançado de tubo, haste, produção de perfil e fornecimento de tarugo de cobre e liga de cobre.Ao alterar a matriz ou usar o método de extrusão de perfuração, várias variedades de ligas e diferentes formatos de seção transversal podem ser extrusadas diretamente.Através da extrusão, a estrutura fundida do lingote é transformada em uma estrutura processada, e o tarugo do tubo extrudado e o tarugo da barra têm alta precisão dimensional e a estrutura é fina e uniforme.O método de extrusão é um método de produção comumente usado por fabricantes nacionais e estrangeiros de tubos e hastes de cobre.
O forjamento de liga de cobre é realizado principalmente por fabricantes de máquinas em meu país, incluindo principalmente forjamento livre e forjamento de matrizes, como engrenagens grandes, engrenagens helicoidais, sem-fim, anéis de engrenagem sincronizadores de automóveis, etc.
O método de extrusão pode ser dividido em três tipos: extrusão direta, extrusão reversa e extrusão especial.Entre elas, existem muitas aplicações de extrusão direta, a extrusão reversa é utilizada na produção de vergalhões e fios de pequeno e médio porte e a extrusão especial é utilizada na produção especial.
Ao extrusar, de acordo com as propriedades da liga, os requisitos técnicos dos produtos extrudados e a capacidade e estrutura da extrusora, o tipo, tamanho e coeficiente de extrusão do lingote devem ser razoavelmente selecionados, de modo que o grau de deformação seja não inferior a 85%.A temperatura e a velocidade de extrusão são os parâmetros básicos do processo de extrusão, e a faixa razoável de temperatura de extrusão deve ser determinada de acordo com o diagrama de plasticidade e o diagrama de fases do metal.Para cobre e ligas de cobre, a temperatura de extrusão é geralmente entre 570 e 950 °C, e a temperatura de extrusão do cobre é até mesmo tão alta quanto 1.000 a 1.050 °C.Comparado com a temperatura de aquecimento do cilindro de extrusão de 400 a 450 °C, a diferença de temperatura entre os dois é relativamente alta.Se a velocidade de extrusão for muito lenta, a temperatura da superfície do lingote cairá muito rápido, resultando em um aumento na irregularidade do fluxo do metal, o que levará a um aumento na carga de extrusão e até mesmo causará um fenômeno de perfuração .Portanto, cobre e ligas de cobre geralmente usam extrusão de velocidade relativamente alta, a velocidade de extrusão pode atingir mais de 50 mm/s.
Quando cobre e ligas de cobre são extrusadas, a extrusão de descascamento é frequentemente usada para remover defeitos superficiais do lingote, e a espessura de descascamento é de 1-2 m.A vedação com água é geralmente usada na saída do tarugo de extrusão, para que o produto possa ser resfriado no tanque de água após a extrusão, e a superfície do produto não seja oxidada, e o processamento a frio subsequente possa ser realizado sem decapagem.Tende a usar uma extrusora de grande tonelagem com um dispositivo de captação síncrona para extrusão de tubos ou bobinas de fio com um peso único superior a 500 kg, de modo a melhorar efetivamente a eficiência da produção e o rendimento abrangente da sequência subsequente.Atualmente, a produção de tubos de cobre e ligas de cobre adota principalmente extrusoras hidráulicas horizontais com sistema de perfuração independente (ação dupla) e transmissão direta da bomba de óleo, e a produção de barras adota principalmente sistema de perfuração não independente (ação única) e transmissão direta da bomba de óleo.Extrusora hidráulica horizontal para frente ou para trás.As especificações de extrusora comumente usadas são de 8 a 50 MN, e agora ela tende a ser produzida por extrusoras de grande tonelagem acima de 40 MN para aumentar o peso único do lingote, melhorando assim a eficiência e o rendimento da produção.
As modernas extrusoras hidráulicas horizontais são estruturalmente equipadas com estrutura integral protendida, guia e suporte do cilindro de extrusão "X", sistema de perfuração integrado, resfriamento interno da agulha de perfuração, conjunto de matrizes deslizantes ou rotativas e dispositivo de troca rápida de matrizes, bomba de óleo variável de alta potência direta acionamento, válvula lógica integrada, controle PLC e outras tecnologias avançadas, o equipamento possui alta precisão, estrutura compacta, operação estável, intertravamento seguro e controle de programa fácil de realizar.A tecnologia de extrusão contínua (Conform) fez alguns progressos nos últimos dez anos, especialmente para a produção de barras de formatos especiais, como fios de locomotivas elétricas, o que é muito promissor.Nas últimas décadas, a nova tecnologia de extrusão desenvolveu-se rapidamente e a tendência de desenvolvimento da tecnologia de extrusão é incorporada da seguinte forma: (1) Equipamento de extrusão.A força de extrusão da prensa extrusora se desenvolverá em uma direção maior, e a prensa extrusora de mais de 30MN se tornará o corpo principal, e a automação da linha de produção da prensa extrusora continuará a melhorar.As máquinas de extrusão modernas adotaram completamente o controle do programa de computador e o controle lógico programável, de modo que a eficiência da produção é bastante melhorada, os operadores são significativamente reduzidos e é até possível realizar a operação automática não tripulada das linhas de produção de extrusão.
A estrutura do corpo da extrusora também foi continuamente melhorada e aperfeiçoada.Nos últimos anos, algumas extrusoras horizontais adotaram uma estrutura protendida para garantir a estabilidade da estrutura geral.A extrusora moderna realiza os métodos de extrusão direta e reversa.A extrusora está equipada com dois eixos de extrusão (eixo de extrusão principal e eixo de matriz).Durante a extrusão, o cilindro de extrusão se move com o eixo principal.Neste momento, o produto é A direção de saída é consistente com a direção de movimento do eixo principal e oposta à direção de movimento relativa do eixo da matriz.A base da matriz da extrusora também adota a configuração de múltiplas estações, o que não só facilita a troca da matriz, mas também melhora a eficiência da produção.As extrusoras modernas usam um dispositivo de controle de ajuste de desvio a laser, que fornece dados eficazes sobre o estado da linha central de extrusão, o que é conveniente para um ajuste rápido e oportuno.A prensa hidráulica de acionamento direto da bomba de alta pressão usando óleo como meio de trabalho substituiu completamente a prensa hidráulica.As ferramentas de extrusão também são constantemente atualizadas com o desenvolvimento da tecnologia de extrusão.A agulha perfurante interna para resfriamento de água foi amplamente promovida, e a agulha perfurante e rolante de seção transversal variável melhora muito o efeito de lubrificação.Moldes cerâmicos e moldes de liga de aço com vida útil mais longa e maior qualidade de superfície são mais amplamente utilizados.
As ferramentas de extrusão também são constantemente atualizadas com o desenvolvimento da tecnologia de extrusão.A agulha perfurante interna para resfriamento de água foi amplamente promovida, e a agulha perfurante e rolante de seção transversal variável melhora muito o efeito de lubrificação.A aplicação de moldes cerâmicos e moldes de liga de aço com maior vida útil e maior qualidade de superfície é mais popular.(2) Processo de produção de extrusão.As variedades e especificações dos produtos extrusados estão em constante expansão.A extrusão de tubos, hastes, perfis e perfis supergrandes de seção pequena e de ultra-alta precisão garante a qualidade da aparência dos produtos, reduz defeitos internos dos produtos, reduz a perda geométrica e promove ainda mais métodos de extrusão, como desempenho uniforme de extrusão produtos.A moderna tecnologia de extrusão reversa também é amplamente utilizada.Para metais facilmente oxidados, é adotada a extrusão de selo d'água, o que pode reduzir a poluição por decapagem, reduzir a perda de metal e melhorar a qualidade da superfície dos produtos.Para produtos extrusados que precisam ser temperados, basta controlar a temperatura adequada.O método de extrusão de selo d'água pode atingir o objetivo, encurtar efetivamente o ciclo de produção e economizar energia.
Com a melhoria contínua da capacidade da extrusora e da tecnologia de extrusão, a moderna tecnologia de extrusão tem sido gradualmente aplicada, como extrusão isotérmica, extrusão de matriz de resfriamento, extrusão de alta velocidade e outras tecnologias de extrusão direta, extrusão reversa, extrusão hidrostática A aplicação prática da tecnologia de extrusão contínua de prensagem e conformação, a aplicação de extrusão de pó e tecnologia de extrusão composta em camadas de materiais supercondutores de baixa temperatura, o desenvolvimento de novos métodos, como extrusão de metal semissólido e extrusão multi-blank, o desenvolvimento de pequenas peças de precisão Tecnologia de formação de extrusão a frio, etc., foram rapidamente desenvolvidos e amplamente desenvolvidos e aplicados.
Espectrômetro
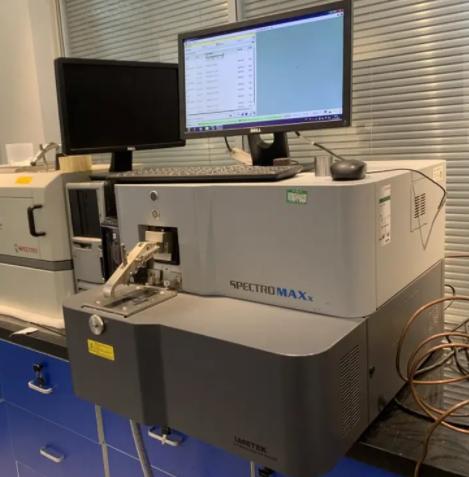
O espectroscópio é um instrumento científico que decompõe luz com composição complexa em linhas espectrais.A luz de sete cores da luz solar é a parte que o olho nu pode distinguir (luz visível), mas se a luz solar for decomposta por um espectrômetro e organizada de acordo com o comprimento de onda, a luz visível ocupa apenas uma pequena faixa no espectro, e o resto são espectros que não podem ser distinguidos a olho nu, como raios infravermelhos, microondas, raios UV, raios X, etc. A informação óptica é captada pelo espectrômetro, revelada com filme fotográfico, ou exibida e analisada por display automático computadorizado instrumento numérico, para detectar quais elementos estão contidos no artigo.Esta tecnologia é amplamente utilizada na detecção de poluição do ar, poluição da água, higiene alimentar, indústria metalúrgica, etc.
O espectrômetro, também conhecido como espectrômetro, é amplamente conhecido como espectrômetro de leitura direta.Um dispositivo que mede a intensidade de linhas espectrais em diferentes comprimentos de onda com fotodetectores, como tubos fotomultiplicadores.Consiste em uma fenda de entrada, um sistema dispersivo, um sistema de imagem e uma ou mais fendas de saída.A radiação eletromagnética da fonte de radiação é separada no comprimento de onda necessário ou região de comprimento de onda pelo elemento dispersivo, e a intensidade é medida no comprimento de onda selecionado (ou varrendo uma determinada banda).Existem dois tipos de monocromadores e policromadores.
Medidor de condutividade de instrumento de teste
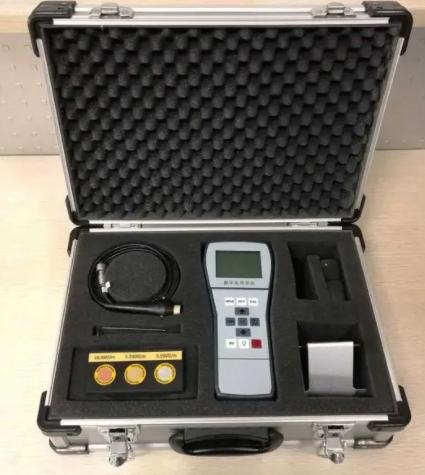
O testador digital portátil de condutividade de metal (medidor de condutividade) FD-101 aplica o princípio de detecção de correntes parasitas e é especialmente projetado de acordo com os requisitos de condutividade da indústria elétrica.Ele atende aos padrões de teste da indústria metalúrgica em termos de função e precisão.
1. O medidor de condutividade de corrente parasita FD-101 tem três exclusivos:
1) O único condutivímetro chinês que passou na verificação do Instituto de Materiais Aeronáuticos;
2) O único medidor de condutividade chinês que pode atender às necessidades das empresas da indústria aeronáutica;
3) O único medidor de condutividade chinês exportado para muitos países.
2. Introdução à função do produto:
1) Grande faixa de medição: 6,9%IACS-110%IACS(4,0MS/m-64MS/m), que atende ao teste de condutividade de todos os metais não ferrosos.
2) Calibração inteligente: rápida e precisa, evitando completamente erros de calibração manual.
3) O instrumento possui boa compensação de temperatura: a leitura é automaticamente compensada para o valor a 20 °C, e a correção não é afetada por erro humano.
4) Boa estabilidade: é sua guarda pessoal para controle de qualidade.
5) Software inteligente humanizado: oferece uma interface de detecção confortável e poderosas funções de processamento e coleta de dados.
6) Operação conveniente: o local de produção e o laboratório podem ser usados em qualquer lugar, conquistando a preferência da maioria dos usuários.
7) Auto-substituição de sondas: Cada host pode ser equipado com várias sondas e os usuários podem substituí-las a qualquer momento.
8) Resolução numérica: 0,1%IACS (MS/m)
9) A interface de medição exibe simultaneamente os valores de medição em duas unidades de %IACS e MS/m.
10) Tem a função de armazenar dados de medição.
Testador de dureza
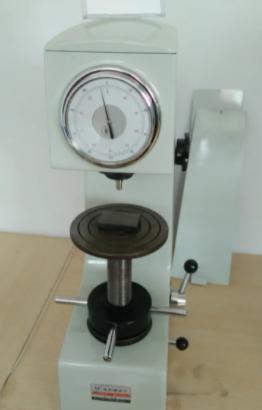
O instrumento adota um design único e preciso em mecânica, óptica e fonte de luz, o que torna a imagem de indentação mais clara e a medição mais precisa.Lentes objetivas de 20x e 40x podem participar da medição, tornando a faixa de medição maior e a aplicação mais extensa.O instrumento está equipado com um microscópio de medição digital, que pode exibir o método de teste, força de teste, comprimento de indentação, valor de dureza, tempo de retenção da força de teste, tempos de medição, etc. na tela do líquido, e possui uma interface rosqueada que pode ser conectada para uma câmera digital e uma câmera CCD.Possui certa representatividade nos principais produtos nacionais.
Testando Detector de Resistividade de Instrumento
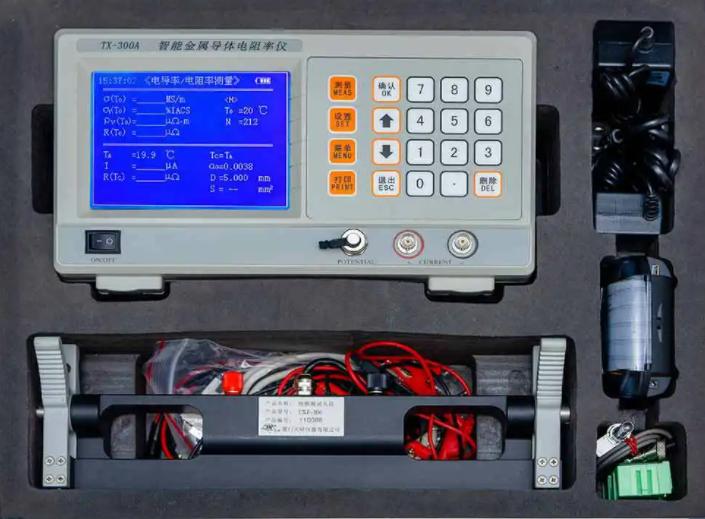
O instrumento de medição de resistividade de fio metálico é um instrumento de teste de alto desempenho para parâmetros como fio, resistividade de barra e condutividade elétrica.Seu desempenho está em total conformidade com os requisitos técnicos relevantes em GB/T3048.2 e GB/T3048.4.Amplamente utilizado em metalurgia, energia elétrica, fios e cabos, eletrodomésticos, faculdades e universidades, unidades de pesquisa científica e outras indústrias.
Principais características do instrumento:
(1) Integra tecnologia eletrônica avançada, tecnologia de chip único e tecnologia de detecção automática, com forte função de automação e operação simples;
(2) Basta pressionar a tecla uma vez, todos os valores medidos podem ser obtidos sem qualquer cálculo, adequados para detecção contínua, rápida e precisa;
(3) Design alimentado por bateria, tamanho pequeno, fácil de transportar, adequado para uso em campo e campo;
(4) Tela grande, fonte grande, pode exibir resistividade, condutividade, resistência e outros valores medidos e temperatura, corrente de teste, coeficiente de compensação de temperatura e outros parâmetros auxiliares ao mesmo tempo, muito intuitivo;
(5) Uma máquina é multifuncional, com 3 interfaces de medição, ou seja, interface de medição de resistividade e condutividade do condutor, interface de medição de parâmetros abrangente de cabo e interface de medição de resistência DC de cabo (tipo TX-300B);
(6) Cada medição tem as funções de seleção automática de corrente constante, comutação automática de corrente, correção automática de ponto zero e correção automática de compensação de temperatura para garantir a precisão de cada valor de medição;
(7) O exclusivo dispositivo de teste portátil de quatro terminais é adequado para medição rápida de diferentes materiais e diferentes especificações de fios ou barras;
(8) Memória de dados integrada, que pode registrar e salvar 1000 conjuntos de dados de medição e parâmetros de medição e conectar-se ao computador superior para gerar um relatório completo.